Did you know we start to mitigate risk in our lives as early as 6 months old? That’s right: at 6 months old, an infant can recognize a stranger and knows – in their gut – that the unfamiliar person could pose a risk. The following cries are the baby’s form of risk mitigation.
But that is exactly how important risk mitigation is: we start practicing it and recognizing the importance of it before we even have conscious thoughts. It’s an instinct.
As we grow, risk mitigation becomes much more comprehensive and different. We practice it in almost every area of our lives: we wear a helmet on a bike, wash our hands before we eat, clean the counters when we cook, etc. We gain the ability to determine what we deem as a risk – and how to mitigate it, even if we do so subconsciously.
Then some of us grow up to work in cleanrooms and we learn the true importance of risk mitigation – and the lives that can be at stake if we don’t pay enough attention to it. Other people’s lives rely on our risk mitigation instincts and knowledge.
We’re here to support you in that endeavor. As clean air experts, we know there are two primary risks in a cleanroom: contamination and data integrity. When either of those are impacted in just about any cleanroom, major problems ensue. That is why we want to talk about a few ways to mitigate risks to your data integrity or contamination risks.
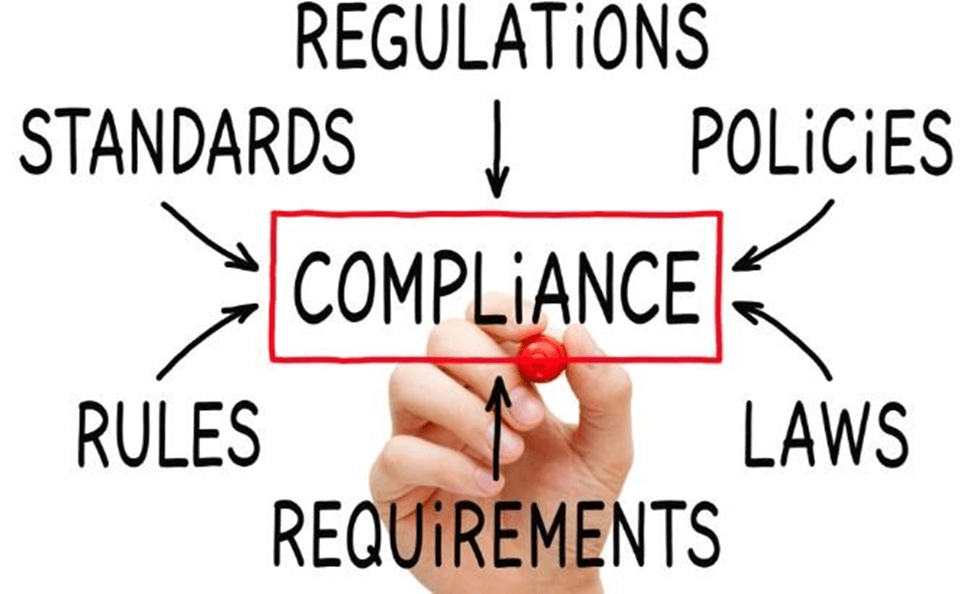
1.Know The Right Regulations Inside And Out
Depending on your cleanroom’s application, you will need to comply with a variety of regulations. These regulations outline how to trace your data, what cleanliness requirements you need to meet, and how to conduct your cleanroom in general.
To mitigate risks to your data and product, you need to stay up to date on these regulations and their best practices. Different organizations release updates for these regulations every few years with new guidance on how to mitigate these risks.
2.Use ALCOA To Trace Your Data
ALCOA stands for Attributable, Legible, Contemporaneous, Original, and Accurate. It is the FDA’s recommendation for the best possible data integrity. In summary, you need to have someone or something to attribute the data to. You need to know where it came from and who is responsible for its accuracy.
The data also must be legible – you need to be able to understand it. If there are symbols, they must be explained and noted.
Next, the data must be contemporaneous, which essentially means it must be recorded when it is gathered.
On top of this, the data must be original or a certified copy. If the data is not original, it is critical you have a good and recorded reason for not having the original data.
Lastly, according to ALCOA, data needs to be an accurate reflection of what happened.
There are a number of systems to record data that aligns with ALCOA, so you have to determine what works for you. But one thing is for certain: abiding by ALCOA guidelines helps mitigate risks associated with data integrity in your cleanroom.
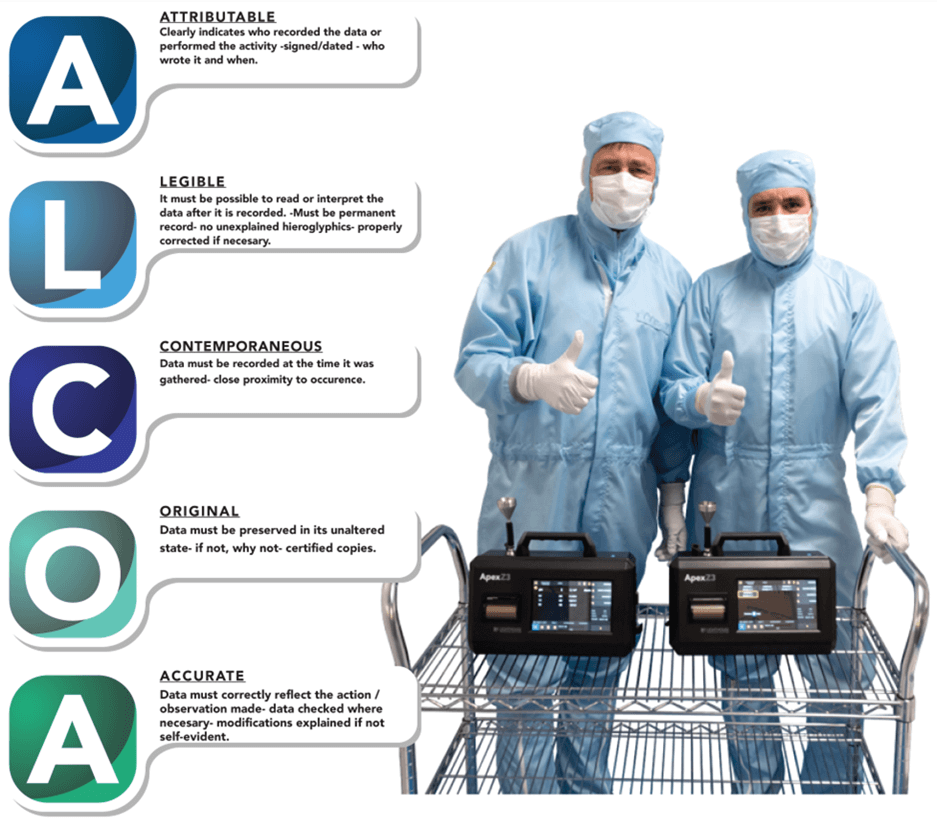
3.Invest In A Real Time Environmental Monitoring System
If you are trying to manually gather, track, and store data according to ALCOA to mitigate risks as much as possible, you are going to have quite the job. Having a computerized system in place to do this for you will go a long way towards freeing up your time and making your life easier. But that is just one benefit of installing a Real Time Environmental Monitoring System (RTEMS).
Not only does a RTEMS help mitigate risks associated with data integrity, they also can help mitigate contamination risks. While they don’t prevent contamination from happening – more on that in a moment – a RTEMS can notify you immediately if there is an error. This prevents downtime and the spread of contamination in your cleanroom. But to truly prevent contamination, you’ll need to address it at the source.
4.Regularly Conduct Gowning Training
Did you know that humans are responsible for up to 80% of particles shed in a cleanroom? That’s right: we’re the problem most of the time. This contamination risk can be mitigated through regular and thorough training.
Too often, we get complacent in our training. We assume that everyone is a pro and they know what they are doing; however, that is neglecting the Forgetting Curve. The Forgetting Curve tells us that we forget up to 90% of something we learn within 7 days of learning it. That is quite disheartening!
But the Forgetting Curve also shows us that reinforcing the information regularly and creatively improves retention. So find creative and regular ways to refresh your employees’ gowning and other training to mitigate contamination risks in your cleanroom!
5.Stay Up To Date On Your Filters
Your first line of defense against contamination in your cleanroom is your filters. They are the guards at the gate. If you neglect regularly changing, cleaning, and monitoring your filters, you will almost surely find your contamination risk increased.
One part of filter maintenance is regularly evaluating your filtration strategy, as well. Are your fine filters, like ULPA and HEPA filters, able to function at their best with your current strategy? Are you providing enough relief for them from larger particles?
If you regularly examine your filters and stay open to new strategy ideas, you will mitigate some contamination risks in your cleanroom.
How Else Can You Mitigate Risks In Your Cleanroom?
Your cleanroom is a fine tuned machine and any number of hiccups could cause major disruptions. We don’t need to tell you what a disruption in a cleanroom can cost you. Thus, investing in risk management and mitigation is a very smart idea.
So where can you get up-to-date information on the best way to manage your cleanroom and mitigate risk? We’ve got your solution: The Lighthouse Knowledge Center.
For over 40 years, we have been the world’s clean air experts. We wanted our knowledge to be available to whoever needed it, so we compiled a hub of information, white papers, instructional videos, and so much more – all for free!
You can create an account today and stay up to date on how best to mitigate risk in your cleanroom.